
Heat Transfer > Internal Cooling Technologies
Internal Cooling Technologies
A typical method for increasing gas turbine performance is to increase the temperature of the flow entering the turbine section. However, increasing the turbine inlet temperature causes problems for the turbine blades. First, the operating temperature of the gas turbine is typically higher than the melting point of turbine blade materials. Secondly, when the local variation of the blade temperature is intensified, thermal stress is generated on the blade. Moreover, when this thermal stress is maintained for a long time, the blade may experience creep.
To combat these issues, turbine blades have complex internal cooling passages which consist of structures to efficiently discharge the heat (Fig. 1). This is referred to as blade internal cooling, and the purpose is to achieve optimal thermal protection while using as little coolant as possible and minimizing the pressure drop of the coolant in the flow path. Fig. 2 shows an actual cross section of a turbine blade, depicting the internal serpentine cooling passages.

(Left) Turbine blade external cooling. (Right) Blade internal cooling.
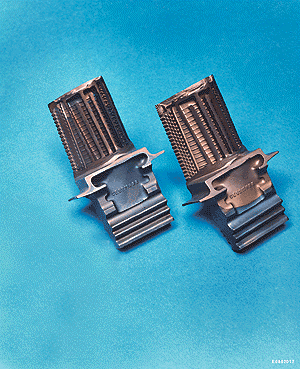