top of page

Turbomachinery > Roughness effects
Surface Roughness Effects on Comporessor and Turbine Aerodynamics
The surface quality in modern gas, steam, and wind turbines are degraded significantly as the service time increases. There are many causes of surface roughness- deposition of the small particles (dust, salt and pollen) and combustion products, surface erosion, and thermal barrier coating spallation. The surface roughness problem has been an important issue due to its unfavorable impacts on the aerodynamic performance and heat transfer.

Picture of a gas turbine for aircraft (GE,www.ge.com)

Picture of a modern gas turbine for power generation (Siemens, www.energy.simens.com)


Roughened compressor (left) and turbine (right) blades in a heavy duty gas turbine
1) Roughness effects on axial turbine performance
This investigation has been made to investigate the surface roughness magnitude and location effects on the axial turbine performance. The impact of surface roughness location (stator vs. rotor, suction side vs. pressure side) on the performance of a single-stage axial turbine has been examined.
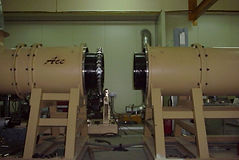

Single stage axial turbine test facility
Sand-roughened turbine rotor blades

Roughness location effect on the turbine efficiency
2) Roughness effects on compressor cascade aerodynamics
Experimental investigations have been conducted to identify roughness effects on compressor cascade aerodynamics, including blade boundary layer development, profile loss, and deviation. This investigation has been conducted at Seoul National University and in collaboration with Professors Knox T. Millsaps and Garth V. Hobson at the Naval Postgraduate School (NPS) in California, USA.
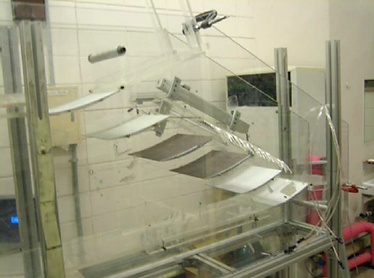
SNU compressor cascade experimental facility
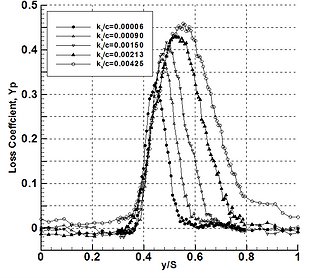
Surface roughness magnitude effect
on loss in SNU cascade

Low-speed cascade wind tunnel facility at the Naval Postgraduate School
(NPS, www.nps.edu)
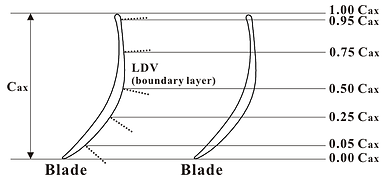
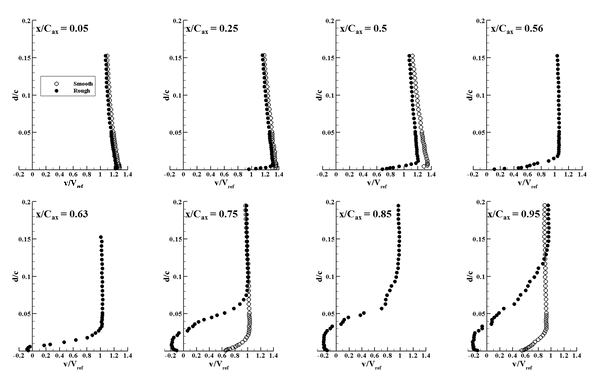
Velocity profiles on blade suction surface (LDV measurement) in NPS cascade.
bottom of page